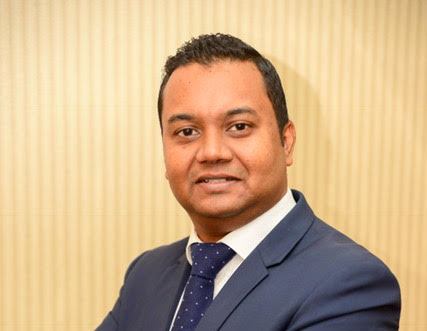
Executive Director
National Productivity and Competitiveness Council (NPCC)
Ever wondered why we get so fussy when it comes to wastages in whatever we do? Indeed, it’s quite logic that anyone wouldn’t like to see them.
Avoiding wastages in any form has always been associated with positive habits that help in leading a better and more organised lifestyle. Whether it is about food, clothing or time, practicing a minimum, if not a zero, degree of wastage makes us more efficient and disciplined while it is also very satisfying. Indeed, a life without wastages is at the end also a productive life.
But as we are so engrossed in our daily routine, we hardly get enough time to ponder where we can really start to avoid the wastages that are hampering on our way to lead a healthy and organised lifestyle. Be it at home or at the office, experts have found seven main areas where wastages occur. This observation can also prompt us to take proper action to avoid wastages in those areas. The seven types of wastages are as follows:
- Defects: Doing a work without any planning which ends up being full of flaws means that you would have to start again. This also means more resources and time to be pumped in again.
- Overproduction: Doing anything over and above what is required is not only a waste of resources but of time that could have been devoted to other productive things.
- Waiting: This element is more felt in a work environment where you depend on a colleague to finish his or her part of the job so that you can do your share on the assignment. Until you have not received anything from them, you are bound to wait, hence a time waste.
- Transportation: Again in a production area, whenever a product is moved unnecessarily, it runs the risk of being damaged, lost or delayed. This definitely does not add any value to any work.
- Inventory: Keeping unused items that are adding to costs in our storeroom, both at home and work, means these are not being of any help to us. Instead, they are adding to costs like storage. Could you perhaps imagine buying surplus perishable goods such as vegetables and not using them?
- Movement: While transportation means damage and transaction costs associated with moving the product, motion rather refers to the damage and costs inflicted on what creates the product. This could be wear and tear for equipment, repetitive injuries for workers and unnecessary downtime.
- Over-processing: Working on something more than is required ends up in taking longer and costing more to produce. This again does not add any value and could turn down a client for a business.
In all, it’s definitely not rocket science to spot down the areas where we could be having non-value adding activities or simply wastes. We just have to sit back a bit and make some observations. And right from there, we can work out how we can reduce and eliminate all the wastes that are keeping us away from a highly productive life!